Den bæredygtige protese
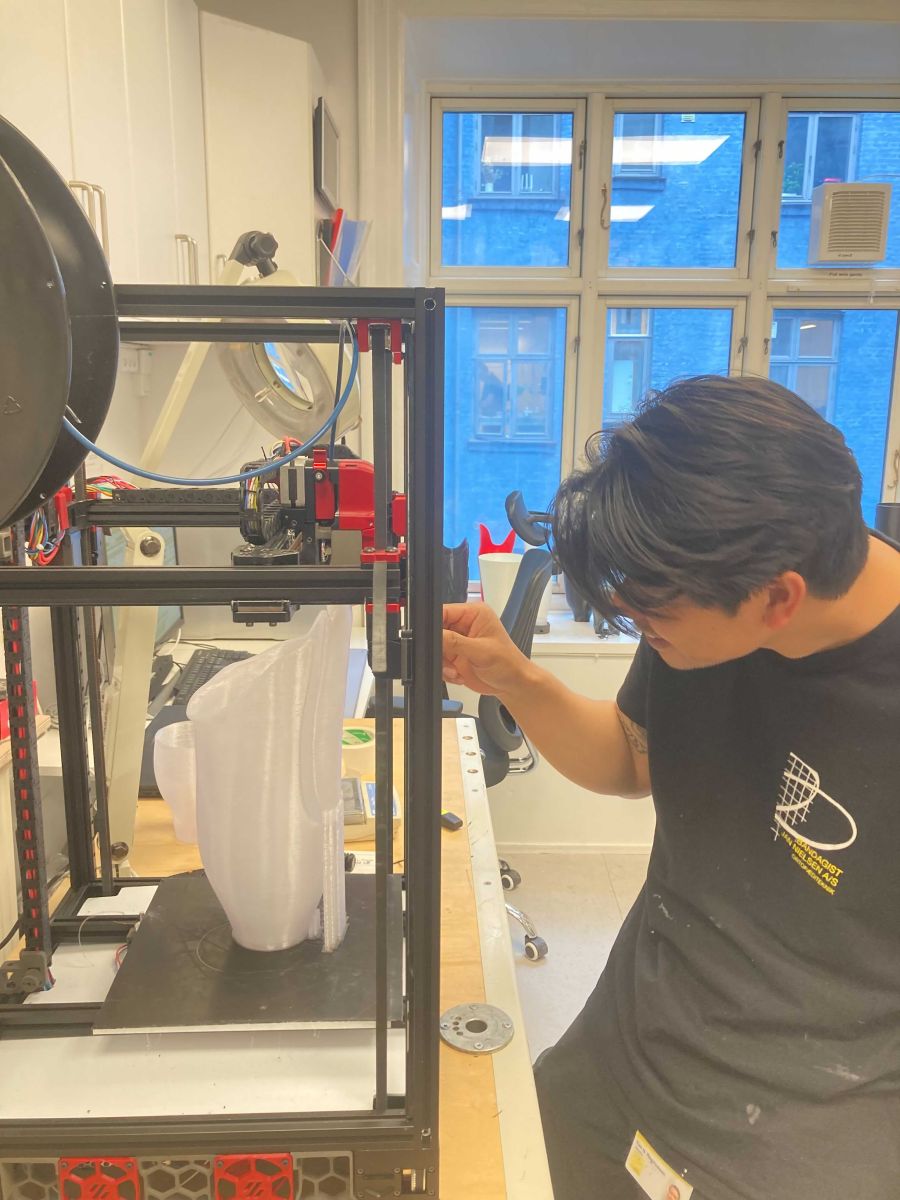
Den bæredygtige protese
Man hører det ofte: jordkloden er under pres, og vi skal tænke over vores klimaaftryk. Nu har Bandagist Jan Nielsen sat fokus på, hvordan tilblivelsen af et protesehylster kan bidrage til reduktionen af CO2
I samarbejde med rådgivningshuset Deloitte, har Bandagist Jan Nielsen regnet på de besparelser, som den nye, bæredygtige produktion medfører. Med udregningerne, som Bandagist Jan Nielsen har vist til Amputations Nyt, fremgår et overordnet fald i kilogram CO2 på 51%, et fald i kubikmeter vand på 34% og dertil et fald kilogram af materialeforbrug på 70%.
Tekst af Laura Hansen
Bæredygtighed er noget, der efterhånden sættes fokus på i alle brancher. Det er muligt at vælge en bæredygtig livsstil, bæredygtige produktioner eller bæredygtige løsninger. Målet er en brug af jordens ressourcer, der skaber balance, så vi ikke ødelægger livsgrundlaget for fremtiden. Og nu kan du altså også vælge en bæredygtig protese.
Hos Bandagist Jan Nielsen på Frederiksborggade i København N, har de brugt tiden under Covid-19 til at blive klogere på, hvordan en bæredygtig protese skabes. De er nu kommet frem til en metode der reducerer produktionen med 51% CO2. Direktør Lisbeth Staxen forklarer om processen, muligheder og den bagvedliggende tankegang til Amputations Nyt.
Pasformen er afgørende,
De fleste må kende til den klassiske metode, hvor bandagisten som det første tager en gipsafstøbning af stumpen, som et testhylster efterfølgende formes ud fra. Ved afstøbningen bruges der gerne tre til fire gipsruller, og det er ikke kun det, som skæres fra, der er materialeaffald. Når det endelige hylster står færdigt kasseres hele afstøbningen.
I dag er gipsafstøbningen hos Bandagist Jan Nielsen sprunget over – i hvert fald hos 90 % af protesebrugerne. Den bæredygtige metode starter med en telefon, der bruges til at skanne det amputerede ben eller arm. Skanningen givet en tredimensional figur af protesebrugeren ben. Ud fra figuren ”modelleres” der efterfølgende det ønskede hylster i et digitalt computerprogram, som til sidst 3D-printes i nylonmateriale. Om processen forklarer Lisbeth Staxen:
”Når det ønskede hylster er formet og rettet ud fra den tredimensionelle figur af vores bandagister, så trykker vi på startknappen, og en af vores 3D-printere sætter i gang. Vi kan printe i lige den farve, det mønster og den tykkelse, som ønskes af brugeren,” men selvom der muligheden for at individualisere hylstrene med små detaljer er en vigtig faktor, så er bæredygtigheden stadig altafgørende.
Fra gips til nylon
51% mindre kilogram CO2 34% mindre kubikmeter vand 70% mindre kilogram materiale
|
men det handler om fremtiden
”Den bæredygtige tanke er en del af vores kultur. Vi har længe haft fokus på genbrug af brugbart materiale, for det er vigtigt, at vi efterlader samfundet så godt, som vi kan. Så da vi deltog i et projekt om digitalisering, som viste dig at gå i en bæredygtig retning, var det helt naturligt for os at følge trop. Som virksomhed skal vi være ansvarlige,” forklarer Lisbeth Staxen.
I samarbejde med rådgivningshuset Deloitte, har Bandagist Jan Nielsen regnet på de besparelser, som den nye, bæredygtige produktion medfører. Med udregningerne, som Bandagist Jan Nielsen har vist til Amputations Nyt, fremgår et overordnet fald i kilogram CO2 på 51%, et fald i kubikmeter vand på 34% og dertil et fald kilogram af materialeforbrug på 70%.
Udregningen er baseret på den nedsatte forbrug af materiale (gips, film, vand mm.) i produktionen, et mindre forbrug af metal, da flere sammensætnings-komponenter bliver unødvendige, og det at det nye nylonmateriale er produceret af bionedbrydeligt amerikansk olie. Udregningerne tager samtidig højde for det forøgede strømforbrug, som den tændte 3D-printer forbruger under produktionen. Strømforbruget er større end ved den traditionelle proces med gipsafstøbning, men det totale CO2 forbrug falder stadig fra 82,3 kilogram til 40,3 kilogram.
Tilfredse brugere
De 3D-printede hylstre og covere er betydeligt lettere end de støbte, og det har de ved Bandagist Jan Nielsen fået positive tilbagemeldinger på. Efter overgangen til 3D-print, lavede de en brugerundersøgelser baseret på svar fra 30 protesebrugere, der viste en positiv tilbagemelding.
”Jeg tror, det i stor grad handler om, at protesebrugerne bare er glade, når den passer. Protesen er kun vigtig og betydningsfuld, når den ikke passer, resten af tiden er det bare en del af hverdagen. Og vi har kun oplevet af den nye teknik har fejlet enkelte gange,” siger direktør Lisbeth Saxsten stolt og tilfreds.
I dag er cirka 90% af Bandagist Jan Nielsens kunder overgået til de bæredygtige hylstre, og Lisbeth Saxsen er sikker på, at det handler om nemhed og bæredygtighed.
”Man skal vælge den nye løsning, fordi man er samfundsborger og tænker på det aftryk man efterlader.”